Destylarka do rozpuszczalnika to urządzenie, które wykorzystuje proces destylacji do oddzielania cieczy na podstawie ich temperatury wrzenia. W praktyce oznacza to, że substancje o różnych temperaturach wrzenia mogą być skutecznie rozdzielane, co jest niezwykle przydatne w laboratoriach chemicznych oraz w przemyśle. Proces ten zaczyna się od podgrzewania mieszaniny, co powoduje, że substancje o niższej temperaturze wrzenia zaczynają parować. Para ta następnie przechodzi przez chłodnicę, gdzie skrapla się z powrotem w ciecz. W ten sposób można uzyskać czysty rozpuszczalnik, który jest wolny od zanieczyszczeń. Warto zaznaczyć, że destylacja może być przeprowadzana w różnych warunkach ciśnienia, co wpływa na efektywność procesu. W przypadku destylarek do rozpuszczalników często stosuje się destylację frakcyjną, która pozwala na bardziej precyzyjne oddzielanie składników.
Jakie są zalety używania destylarki do rozpuszczalnika
Używanie destylarki do rozpuszczalnika niesie ze sobą wiele korzyści, które sprawiają, że jest to urządzenie niezwykle popularne zarówno w laboratoriach, jak i w przemyśle chemicznym. Przede wszystkim, destylacja pozwala na uzyskanie wysokiej czystości substancji, co jest kluczowe w wielu procesach produkcyjnych oraz badawczych. Dzięki temu można uniknąć kontaminacji i uzyskać wyniki badań o większej wiarygodności. Kolejną zaletą jest możliwość wielokrotnego użycia rozpuszczalników, co przyczynia się do zmniejszenia kosztów operacyjnych oraz ograniczenia ilości odpadów chemicznych. Destylarki są również stosunkowo łatwe w obsłudze i mogą być dostosowane do różnych potrzeb użytkowników. Wiele nowoczesnych modeli wyposażonych jest w automatyczne systemy monitorowania i kontroli procesu, co zwiększa bezpieczeństwo pracy oraz efektywność działania.
Jakie rodzaje destylarek do rozpuszczalnika są dostępne na rynku
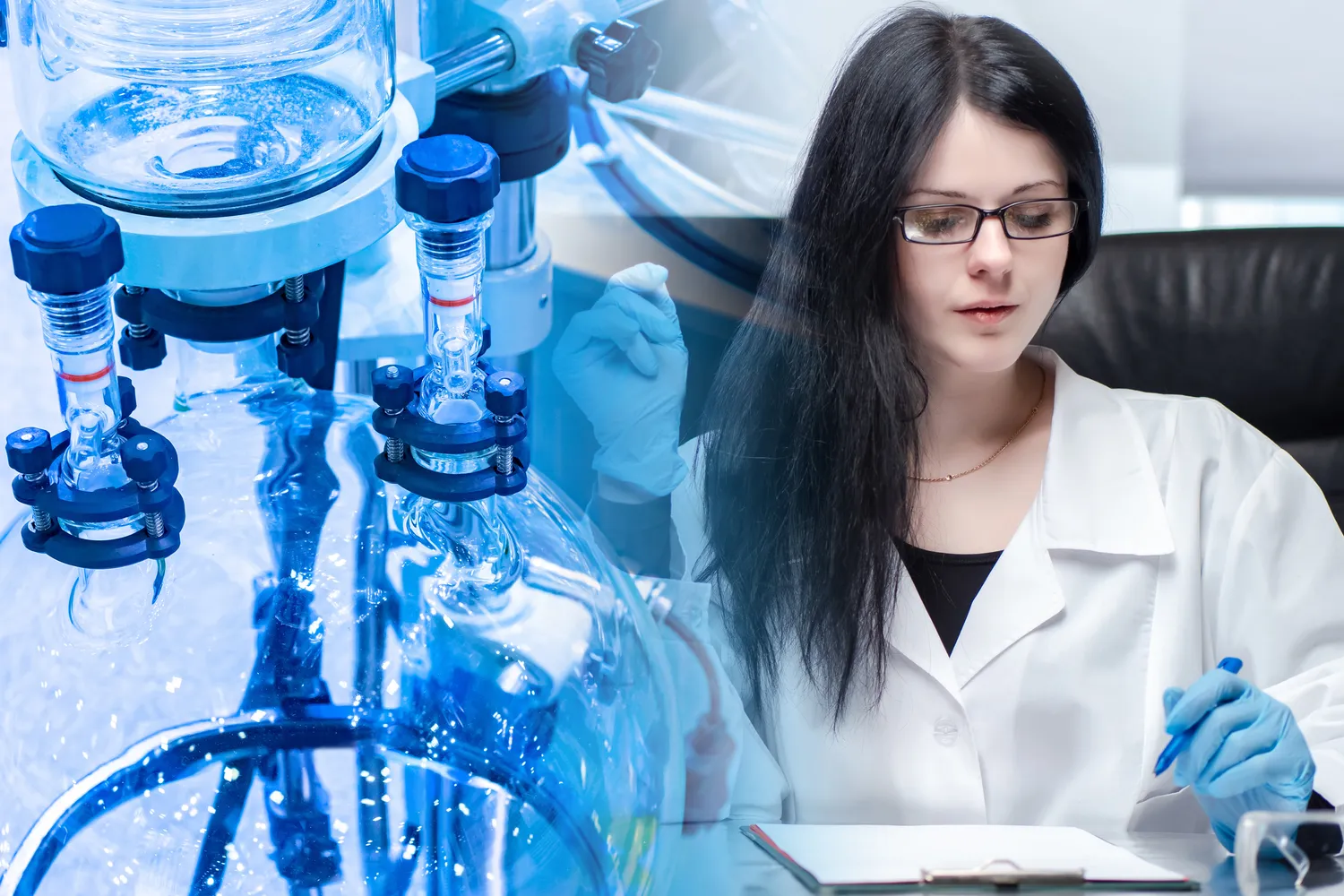
Na rynku dostępnych jest wiele różnych rodzajów destylarek do rozpuszczalników, które różnią się zarówno budową, jak i zastosowaniem. Najpopularniejsze modele to destylarki prostoliniowe oraz frakcyjne. Destylarki prostoliniowe są najprostsze w konstrukcji i idealnie nadają się do podstawowych procesów destylacji. Z kolei destylarki frakcyjne umożliwiają bardziej zaawansowane separacje dzięki zastosowaniu kolumny frakcyjnej, co pozwala na uzyskanie wyższej czystości produktów końcowych. Innym typem są destylarki rotacyjne, które są często wykorzystywane w laboratoriach chemicznych do delikatnej destylacji substancji termolabilnych. Oprócz tego istnieją także destylarki próżniowe, które działają w obniżonym ciśnieniu i umożliwiają destylację substancji o wysokich temperaturach wrzenia bez ryzyka ich degradacji.
Jakie zastosowania ma destylarka do rozpuszczalnika w przemyśle
Destylarka do rozpuszczalnika znajduje szerokie zastosowanie w różnych branżach przemysłowych, co czyni ją niezbędnym narzędziem dla wielu przedsiębiorstw. W przemyśle chemicznym służy głównie do oczyszczania surowców oraz odzyskiwania cennych substancji chemicznych z odpadów produkcyjnych. Dzięki procesowi destylacji możliwe jest uzyskanie wysokiej jakości rozpuszczalników, które mogą być ponownie wykorzystane w produkcji. W branży farmaceutycznej destylarki są wykorzystywane do przygotowywania czystych substancji czynnych oraz ekstraktów roślinnych. W laboratoriach analitycznych natomiast służą do przygotowywania próbek do badań oraz analiz chemicznych. Ponadto, w przemyśle spożywczym stosuje się je do produkcji alkoholi oraz innych napojów fermentowanych.
Jakie czynniki wpływają na wybór destylarki do rozpuszczalnika
Wybór odpowiedniej destylarki do rozpuszczalnika jest kluczowy dla efektywności procesu destylacji oraz jakości uzyskiwanych produktów. Istnieje wiele czynników, które należy wziąć pod uwagę przy podejmowaniu decyzji. Przede wszystkim, istotna jest skala produkcji, ponieważ różne modele destylarek są zaprojektowane z myślą o różnych wielkościach operacji. Małe laboratoria mogą potrzebować kompaktowych modeli, które zajmują mniej miejsca, podczas gdy większe zakłady przemysłowe mogą wymagać bardziej zaawansowanych systemów o dużej wydajności. Kolejnym czynnikiem jest rodzaj substancji, które mają być destylowane. Niektóre rozpuszczalniki mogą wymagać specjalnych warunków pracy, takich jak obniżone ciśnienie czy kontrolowana temperatura, co powinno być uwzględnione przy wyborze urządzenia. Ważne są także aspekty związane z bezpieczeństwem i łatwością obsługi. Nowoczesne destylarki często wyposażone są w systemy automatyzacji oraz monitorowania, co zwiększa bezpieczeństwo pracy i ułatwia codzienną eksploatację.
Jakie są najczęstsze problemy z destylarką do rozpuszczalnika
Podczas użytkowania destylarki do rozpuszczalnika mogą wystąpić różnorodne problemy, które mogą wpływać na efektywność procesu oraz jakość uzyskiwanych produktów. Jednym z najczęstszych problemów jest niewłaściwe ustawienie temperatury, co może prowadzić do niepełnej destylacji lub kontaminacji produktu końcowego. W przypadku destylacji frakcyjnej ważne jest odpowiednie dobranie kolumny frakcyjnej oraz jej parametrów pracy, aby uzyskać pożądany stopień separacji składników. Innym problemem mogą być zatory w systemie chłodzenia, które prowadzą do nieefektywnego skraplania pary i obniżenia wydajności urządzenia. Regularne czyszczenie i konserwacja destylarki są kluczowe dla utrzymania jej w dobrym stanie technicznym. Często zdarzają się również problemy związane z uszczelnieniami i połączeniami, które mogą prowadzić do wycieków substancji chemicznych. W takich przypadkach konieczne jest natychmiastowe działanie w celu zapewnienia bezpieczeństwa użytkowników oraz ochrony środowiska.
Jakie materiały są najczęściej używane w budowie destylarek
Materiały używane do budowy destylarek do rozpuszczalników mają kluczowe znaczenie dla ich wydajności oraz trwałości. Najczęściej stosowanym materiałem jest stal nierdzewna, która charakteryzuje się wysoką odpornością na korozję oraz chemikalia. Dzięki tym właściwościom stal nierdzewna zapewnia długotrwałe użytkowanie urządzenia bez ryzyka degradacji materiału. W przypadku elementów narażonych na działanie wysokich temperatur często stosuje się szkło borokrzemowe, które ma doskonałe właściwości termiczne i chemiczne. Szkło to jest szczególnie cenione w laboratoriach chemicznych ze względu na swoją przejrzystość oraz łatwość w monitorowaniu procesów zachodzących wewnątrz urządzenia. Dodatkowo, niektóre modele destylarek wykorzystują materiały kompozytowe lub teflonowe w miejscach narażonych na intensywne działanie substancji chemicznych. Tego rodzaju materiały mają na celu zwiększenie bezpieczeństwa użytkowania oraz minimalizację ryzyka kontaminacji produktów końcowych.
Jakie są nowoczesne technologie w destylarkach do rozpuszczalnika
Nowoczesne technologie w dziedzinie destylacji znacznie poprawiły efektywność i bezpieczeństwo pracy z destylarkami do rozpuszczalników. Wiele współczesnych modeli wyposażonych jest w zaawansowane systemy automatyzacji, które umożliwiają precyzyjne kontrolowanie parametrów procesu, takich jak temperatura czy ciśnienie. Dzięki tym technologiom możliwe jest uzyskanie stabilnych warunków pracy oraz minimalizacja ryzyka błędów ludzkich. Dodatkowo, nowoczesne destylarki często posiadają funkcje monitorowania w czasie rzeczywistym, co pozwala na bieżąco śledzenie postępu procesu oraz identyfikowanie potencjalnych problemów jeszcze przed ich wystąpieniem. Innowacyjne rozwiązania obejmują również zastosowanie technologii odzysku ciepła, która pozwala na zwiększenie efektywności energetycznej procesu destylacji poprzez ponowne wykorzystanie ciepła generowanego podczas pracy urządzenia.
Jakie są najlepsze praktyki użytkowania destylarki do rozpuszczalnika
Aby maksymalnie wykorzystać potencjał destylarki do rozpuszczalnika oraz zapewnić jej długotrwałe i bezpieczne działanie, warto przestrzegać kilku najlepszych praktyk użytkowania tego urządzenia. Przede wszystkim należy regularnie przeprowadzać konserwację i czyszczenie wszystkich elementów urządzenia zgodnie z zaleceniami producenta. Utrzymanie czystości nie tylko zwiększa efektywność działania destylarki, ale także minimalizuje ryzyko kontaminacji produktów końcowych. Ważne jest również dokładne monitorowanie parametrów pracy podczas procesu destylacji, aby uniknąć sytuacji prowadzących do niepełnej separacji składników lub uszkodzenia sprzętu. Należy także zwracać uwagę na jakość używanych surowców i rozpuszczalników, ponieważ ich zanieczyszczenia mogą negatywnie wpłynąć na wyniki procesu. Kolejną istotną kwestią jest przestrzeganie zasad bezpieczeństwa podczas obsługi urządzenia – należy stosować odpowiednie środki ochrony osobistej oraz dbać o wentylację pomieszczeń roboczych.
Jakie są przyszłościowe kierunki rozwoju technologii destylacyjnych
Przyszłość technologii destylacyjnych zapowiada się obiecująco dzięki ciągłemu postępowi naukowemu oraz innowacjom technologicznym w dziedzinie chemii i inżynierii procesowej. Jednym z głównych kierunków rozwoju jest zwiększenie efektywności energetycznej procesów destylacyjnych poprzez zastosowanie nowych materiałów izolacyjnych oraz technologii odzysku ciepła. Ponadto rozwijane są nowe metody separacji substancji chemicznych, takie jak membranowa separacja czy ekstrakcja cieczy cieczą, które mogą stanowić alternatywę dla tradycyjnej destylacji i oferować lepsze wyniki w niektórych zastosowaniach przemysłowych. W kontekście ochrony środowiska rośnie zainteresowanie technologiami zielonej chemii, które mają na celu minimalizację zużycia rozpuszczalników organicznych oraz redukcję odpadów chemicznych powstających podczas procesów produkcyjnych. Również automatyzacja procesów produkcyjnych staje się coraz bardziej powszechna – inteligentne systemy zarządzania danymi będą miały kluczowe znaczenie dla optymalizacji procesów oraz poprawy jakości produktów końcowych.