
Budowa maszyn pneumatycznych opiera się na kilku kluczowych elementach, które współpracują ze sobą, aby zapewnić efektywne działanie systemu. Podstawowym komponentem jest sprężarka, która odpowiada za wytwarzanie sprężonego powietrza. Sprężarki mogą być różnego rodzaju, w tym tłokowe, śrubowe czy wirnikowe, a ich wybór zależy od specyficznych potrzeb aplikacji. Kolejnym istotnym elementem są zbiorniki ciśnieniowe, które magazynują sprężone powietrze i umożliwiają jego późniejsze wykorzystanie. Zbiorniki te muszą być odpowiednio zaprojektowane i wykonane z materiałów odpornych na wysokie ciśnienie, aby zapewnić bezpieczeństwo użytkowania. W systemie pneumatycznym niezbędne są także zawory, które kontrolują przepływ powietrza oraz jego kierunek. Zawory mogą być ręczne lub automatyczne, a ich wybór wpływa na precyzję i szybkość działania całego układu. Oprócz tych elementów, ważne są również siłowniki pneumatyczne, które przekształcają energię sprężonego powietrza w ruch mechaniczny. Siłowniki te mogą mieć różne kształty i rozmiary, co pozwala na ich zastosowanie w różnych aplikacjach przemysłowych.
Jakie są zalety i wady maszyn pneumatycznych w przemyśle
Maszyny pneumatyczne cieszą się dużą popularnością w przemyśle ze względu na swoje liczne zalety, ale mają także pewne ograniczenia. Jedną z głównych zalet jest ich prostota konstrukcji oraz łatwość w obsłudze. Dzięki temu operatorzy mogą szybko nauczyć się korzystać z takich urządzeń, co przekłada się na efektywność pracy. Ponadto maszyny pneumatyczne charakteryzują się dużą mocą przy stosunkowo niewielkiej wadze, co czyni je idealnymi do zastosowań mobilnych oraz w miejscach o ograniczonej przestrzeni. Dodatkowo systemy pneumatyczne są mniej podatne na uszkodzenia mechaniczne niż ich elektryczne odpowiedniki, co zwiększa ich niezawodność. Jednakże maszyny te mają również swoje wady. Przede wszystkim wymagają dostępu do źródła sprężonego powietrza, co może być problematyczne w niektórych lokalizacjach. Ponadto sprężone powietrze może być kosztowne w produkcji i utrzymaniu, zwłaszcza jeśli system nie jest odpowiednio zoptymalizowany. Innym ograniczeniem jest to, że siła generowana przez maszyny pneumatyczne może być trudna do precyzyjnego kontrolowania w porównaniu do systemów elektrycznych czy hydraulicznych.
Jakie zastosowania znajdują maszyny pneumatyczne w różnych branżach
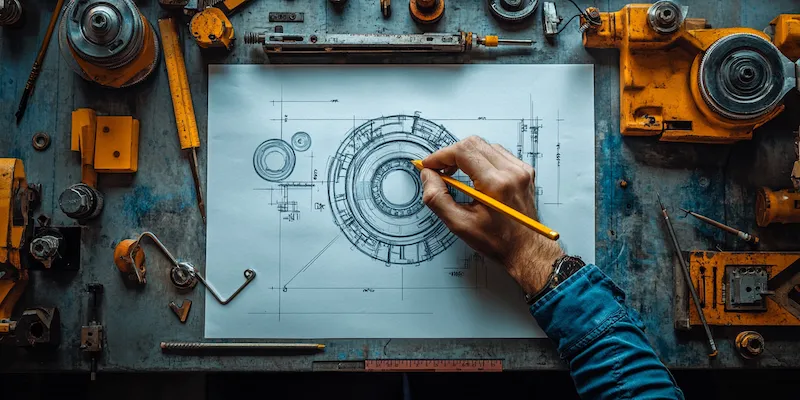
Maszyny pneumatyczne znajdują szerokie zastosowanie w różnych branżach przemysłowych dzięki swojej wszechstronności i efektywności. W przemyśle motoryzacyjnym są wykorzystywane do montażu części oraz w procesach lakierniczych, gdzie precyzyjne natryskiwanie farby jest kluczowe dla jakości wykończenia. W branży spożywczej maszyny te służą do pakowania produktów oraz transportu surowców między różnymi etapami produkcji. Dzięki zastosowaniu technologii pneumatycznej możliwe jest zachowanie higieny oraz minimalizacja ryzyka kontaminacji żywności. W sektorze budowlanym maszyny pneumatyczne są używane do narzędzi takich jak młoty udarowe czy wiertnice, które umożliwiają szybkie i efektywne wykonywanie prac budowlanych. Również w logistyce i magazynowaniu maszyny te odgrywają kluczową rolę; stosowane są do podnoszenia i przenoszenia ciężkich ładunków za pomocą siłowników pneumatycznych. W branży elektronicznej maszyny pneumatyczne wspierają procesy montażu komponentów oraz testowania produktów końcowych.
Jakie innowacje wpływają na rozwój technologii maszyn pneumatycznych
W ostatnich latach technologia maszyn pneumatycznych przechodzi dynamiczny rozwój dzięki innowacjom technologicznym oraz rosnącemu zainteresowaniu automatyzacją procesów przemysłowych. Jednym z najważniejszych trendów jest integracja systemów pneumatycznych z nowoczesnymi rozwiązaniami cyfrowymi, takimi jak Internet Rzeczy (IoT). Dzięki temu możliwe jest monitorowanie stanu maszyn w czasie rzeczywistym oraz optymalizacja ich pracy poprzez analizę danych zbieranych podczas eksploatacji. Innowacyjne czujniki pozwalają na dokładniejsze pomiary ciśnienia czy przepływu powietrza, co przekłada się na lepszą kontrolę nad procesami produkcyjnymi. Kolejnym ważnym aspektem jest rozwój materiałów używanych do produkcji elementów maszyn pneumatycznych; nowoczesne tworzywa sztuczne oraz kompozyty charakteryzują się mniejszą wagą oraz większą odpornością na korozję i zużycie. Dodatkowo coraz więcej producentów stawia na energooszczędność swoich urządzeń; nowe modele sprężarek czy siłowników oferują znacznie wyższą wydajność przy mniejszym zużyciu energii.
Jakie są kluczowe czynniki wpływające na efektywność maszyn pneumatycznych
Efektywność maszyn pneumatycznych jest determinowana przez szereg kluczowych czynników, które mają bezpośredni wpływ na ich wydajność oraz niezawodność. Przede wszystkim istotne jest odpowiednie dobranie komponentów systemu, takich jak sprężarki, zawory czy siłowniki. Wybór elementów o wysokiej jakości oraz dostosowanych do specyficznych wymagań aplikacji pozwala na optymalizację pracy całego układu. Kolejnym czynnikiem jest właściwe utrzymanie i konserwacja maszyn; regularne przeglądy oraz czyszczenie filtrów powietrza mogą znacząco wpłynąć na wydajność systemu. Niezwykle ważne jest także monitorowanie ciśnienia roboczego w układzie; zbyt niskie lub zbyt wysokie ciśnienie może prowadzić do nieefektywnego działania maszyn oraz zwiększonego zużycia energii. Oprócz tego, odpowiednie szkolenie operatorów ma kluczowe znaczenie dla prawidłowego użytkowania maszyn pneumatycznych. Operatorzy powinni być świadomi zasad działania systemu oraz umieć rozpoznawać potencjalne problemy, co przyczynia się do szybszej reakcji na awarie i minimalizacji przestojów.
Jakie są najczęstsze problemy związane z maszynami pneumatycznymi
Maszyny pneumatyczne, mimo swoich licznych zalet, mogą napotykać różnorodne problemy, które wpływają na ich działanie i efektywność. Jednym z najczęstszych problemów jest wyciek sprężonego powietrza, który może prowadzić do znacznych strat energetycznych oraz obniżenia wydajności systemu. Wyciek ten często występuje w miejscach połączeń elementów układu, takich jak węże czy złączki, dlatego regularne kontrole stanu tych komponentów są niezwykle istotne. Innym powszechnym problemem jest zanieczyszczenie sprężonego powietrza, które może prowadzić do uszkodzenia elementów maszyn oraz obniżenia jakości produkcji. Zastosowanie odpowiednich filtrów oraz systemów osuszania powietrza pomaga w eliminacji tego problemu. Problemy z ciśnieniem roboczym również mogą negatywnie wpłynąć na działanie maszyn pneumatycznych; zarówno zbyt niskie, jak i zbyt wysokie ciśnienie mogą prowadzić do nieprawidłowego funkcjonowania siłowników czy zaworów. Warto również zwrócić uwagę na hałas generowany przez maszyny pneumatyczne; nadmierny hałas może być nie tylko uciążliwy dla operatorów, ale także wskazywać na problemy mechaniczne wymagające interwencji.
Jakie są przyszłe kierunki rozwoju technologii maszyn pneumatycznych
Przyszłość technologii maszyn pneumatycznych zapowiada się obiecująco dzięki ciągłemu rozwojowi innowacyjnych rozwiązań oraz rosnącemu zainteresowaniu automatyzacją procesów przemysłowych. Jednym z głównych kierunków rozwoju jest dalsza integracja systemów pneumatycznych z technologią IoT, co umożliwi jeszcze bardziej zaawansowane monitorowanie i zarządzanie procesami produkcyjnymi. Dzięki zastosowaniu inteligentnych czujników i algorytmów analizy danych możliwe będzie przewidywanie awarii oraz optymalizacja pracy urządzeń w czasie rzeczywistym. Również rozwój sztucznej inteligencji ma potencjał do rewolucjonizowania sposobu zarządzania systemami pneumatycznymi; AI może pomóc w automatyzacji procesów diagnostycznych oraz podejmowaniu decyzji dotyczących konserwacji i eksploatacji maszyn. Kolejnym ważnym trendem jest dążenie do zwiększenia efektywności energetycznej systemów pneumatycznych; nowoczesne technologie sprężarek i siłowników będą projektowane tak, aby minimalizować zużycie energii przy jednoczesnym zachowaniu wysokiej wydajności. Warto również zauważyć rosnącą popularność rozwiązań hybrydowych łączących technologie pneumatyczne z hydraulicznymi czy elektrycznymi; takie podejście pozwala na uzyskanie jeszcze lepszych parametrów pracy oraz większej elastyczności zastosowań w różnych branżach przemysłowych.
Jakie są koszty związane z użytkowaniem maszyn pneumatycznych
Koszty związane z użytkowaniem maszyn pneumatycznych mogą być różnorodne i zależą od wielu czynników, takich jak rodzaj zastosowania, intensywność eksploatacji czy jakość używanych komponentów. Podstawowym kosztem jest energia potrzebna do wytwarzania sprężonego powietrza; cena energii elektrycznej oraz efektywność sprężarki mają kluczowe znaczenie dla całkowitych wydatków operacyjnych. Warto również uwzględnić koszty związane z konserwacją i serwisowaniem maszyn; regularne przeglądy oraz wymiana zużytych części są niezbędne dla zapewnienia niezawodności i długowieczności urządzeń. Koszty zakupu sprzętu również mogą być znaczące; inwestycja w wysokiej jakości maszyny pneumatyczne może być wysoka, ale często przekłada się na niższe koszty eksploatacyjne w dłuższej perspektywie czasowej. Ponadto warto pamiętać o kosztach związanych z szkoleniem operatorów; odpowiednie przygotowanie personelu ma kluczowe znaczenie dla efektywnego wykorzystania maszyn oraz minimalizacji ryzyka awarii. Nie można zapominać o kosztach związanych z ewentualnymi przestojami spowodowanymi awariami czy niesprawnością sprzętu; takie sytuacje mogą prowadzić do znacznych strat finansowych dla przedsiębiorstw.
Jakie są najnowsze trendy w projektowaniu maszyn pneumatycznych
Najnowsze trendy w projektowaniu maszyn pneumatycznych koncentrują się na innowacyjności, efektywności energetycznej oraz dostosowywaniu urządzeń do zmieniających się potrzeb rynku przemysłowego. Coraz większy nacisk kładzie się na miniaturyzację komponentów, co pozwala na tworzenie bardziej kompaktowych i wszechstronnych rozwiązań. Dzięki temu maszyny pneumatyczne mogą być stosowane w miejscach o ograniczonej przestrzeni, a ich mobilność staje się kluczowym atutem w wielu branżach. Kolejnym istotnym trendem jest rozwój technologii cyfrowych; nowoczesne maszyny wyposażane są w systemy monitorujące ich stan oraz wydajność w czasie rzeczywistym. Umożliwia to szybką reakcję na ewentualne problemy oraz optymalizację procesów produkcyjnych poprzez analizę danych zbieranych podczas eksploatacji. Również aspekty ekologiczne stają się coraz ważniejsze; projektanci starają się tworzyć maszyny o mniejszym wpływie na środowisko poprzez zastosowanie materiałów biodegradowalnych oraz energooszczędnych rozwiązań technologicznych. Dodatkowo rośnie zainteresowanie rozwiązaniami hybrydowymi łączącymi technologie pneumatyczne z elektrycznymi lub hydraulicznymi; takie podejście pozwala na uzyskanie lepszych parametrów pracy oraz większej elastyczności zastosowań.